A289 Grade 18Mn18Cr Forged ring
2025-02-20 16:36:00 Origin: Remark:0 Click:
18Mn18Cr nonmagnetic steel is Alloy Steel Forgings for Nonmagnetic Retaining Rings for Generator Such main nonmagnetic materials (1)Mn18Cr18 (2)18Mn18Cr (3)P900
Such main nonmagnetic materials are available as:
(1) Mn18Cr18 (2) 18Mn18Cr (3) P900 (4) 50Mn18Cr5 (5) 50Mn18Cr4WN
(1) Mn18Cr18 (2) 18Mn18Cr (3) P900 (4) 50Mn18Cr5 (5) 50Mn18Cr4WN
1. Key feature
Nonmagnetic retaining ring is a critical component of heavy turbonator, one of the components bearing the highest stress, and by means of the retaining ring the centrifugal force is borne on the location of turning of the coil block on the both ends of the rotor.
2. Characteristics:
The retaining ring is hot assembled on the both ends of the rotors to compact the coils on the ends to prevent the coils of rotors during high speed operation from runaway damages which might cause disastrous accidents to the power stations.
3.Grades:
Unique heavy retaining ring presses are available, they possess the following grades for mechanical properties
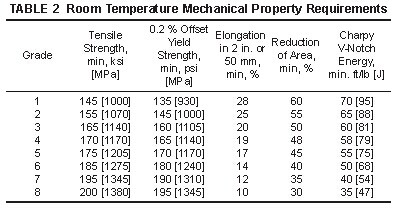
4. Manufacture
The steel shall be made by the electro-slag-remelt (ESR)process. The electrodes shall be made by either the basic electric furnace or ladle refining processes.
Sufficient discard shall be taken from each ingot to secure freedom from piping and undue segregation.
Forged rings shall be solution treated following hot working and prior to the cold expansion procedure.
Rings shall be rough machined prior to cold expansion or final heat treatment.
Rings shall be expanded by an appropriate method such as segmented dies, tapered plug, etc. in the temperature range of 60 to 390°F [15 to 200°C] in order to develop the required tensile properties.
After cold expansion, the rings shall be heated to between 575 and 750°F [300 to 400°C] at a rate not to exceed 75°F [40°C]/h, held at this temperature for 6 to 12 h, and then slow cooled to ambient temperature.
The steel shall be made by the electro-slag-remelt (ESR)process. The electrodes shall be made by either the basic electric furnace or ladle refining processes.
Sufficient discard shall be taken from each ingot to secure freedom from piping and undue segregation.
Forged rings shall be solution treated following hot working and prior to the cold expansion procedure.
Rings shall be rough machined prior to cold expansion or final heat treatment.
Rings shall be expanded by an appropriate method such as segmented dies, tapered plug, etc. in the temperature range of 60 to 390°F [15 to 200°C] in order to develop the required tensile properties.
After cold expansion, the rings shall be heated to between 575 and 750°F [300 to 400°C] at a rate not to exceed 75°F [40°C]/h, held at this temperature for 6 to 12 h, and then slow cooled to ambient temperature.
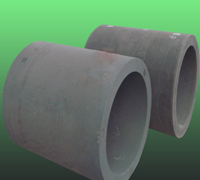
Hot search:ASTM A289 Grade 18Mn18Cr ring
Previous page:1.4550 /DIN X6CrNiNb18-10
Last page:X2NiCrAlTi32-20
Total list
Monthly rank
- 6X22CrMoV12-1 +QT1
- 5M-152 / S64152 / 1.4938 Forgings
- 5ASTM A565 Grade 615
- 4AMS 5622 / 17-4PH / SS630 Forgings
- 4AISI 630 & 17-4PH & 1.4542 & S17400 Aging Steel
- 4SAE 51430 Ferritic Stainless Steel
- 4A289 Grade 18Mn18Cr Forged ring
- 3X50NiCrWV13-13 ESR Ingot, 1.2731 Forgings
- 3S13800 bar, S13800 plate
- 3FV520B Martensitic Aging Steel